Susan Gordon, Business Reporter 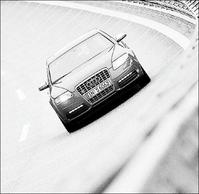
THE SEASONALLY POPULAR two-door Island Cruisers motor car, first built in 1999, is one of the many attempts made by Jamaica to manufacture motor vehicles. In that particular attempt, German automotive engineering was sought.
Today, Jamaicans, according to industry source, import 19,000 vehicles per annum with the audacious Audi being among them, but few ever get behind the manufacturing process of these automobiles.
On a recent visit to Audi's design headquarters in Ingolstadt Germany, The Sunday Gleaner got an idea of how Audis were designed and manufactured. Audi's car designs are developed three years ahead of time to capture the progressive, sporty or classic theme. Its 160-member design headquarters headed by Valter De'Silva holds to the maxim "'icons for tomorrow".
The group relies on people in the fashion and furniture fields for feedback. "We sold up to 7.0 per cent in white cars," said the presenter.
Steps in Manufacturing
Preparing the model: The launch of the design is about 23 months before the launch of production, but the entire production process has a time line of 54 months. The models of the designs are done in clay and the detailed interior designs, including the engine department, are done in graphics, but the cover up is done in clay that is sometimes painted. In the end, the clay model is covered with a piece of foil giving it a real model look.
Producing the car: There are five lines of production in the manufacturing process, which takes between 36 and 38 hours. For aluminium cars it takes up to six days to produce a single unit.
Stage one - The metals are cut into planks and at a pressure of 7,300 tonnes is pressed into parts. The metal is protected with a special grease material and for the outside, a galvanised material is used with an electro thickness of between 0.3 to 0.6 mm.
Stage two - Audi uses 95 per cent robots each costing about Euro 1 million to assemble the parts and form the body. The robots purchased from the manufacturing company called KUKAS have an individualised programme and know which type of cars to be made.
Stage three - Cars receive four layers of paint or colouring which achieves the thickness of a "hair's breadth". This takes about 10 hours. The electrochemical coating in the second stage of colouring helps to prevent corrosion.
A special substance in the paint produces special effects on how the lights reflect from the different points on the car. A product called Colour Care measures the colours and shades on the car. It is a worldwide colour software, which was co-developed by Audi. Thickness of the paint is also measured by software.
Stage four - cars are hung and the body or shell is fitted with the chassis. This stage, called the marriage, takes 90 seconds per unit.
Stage five - There is a line for wheels and lights. The doors and tyres, etc., are fit in.
Finally, a customer in Germany can go straight to the factory to buy his or her car after making a full deposit on the vehicle.